Zhafir Boosts Optical Excellence
2024-07-23
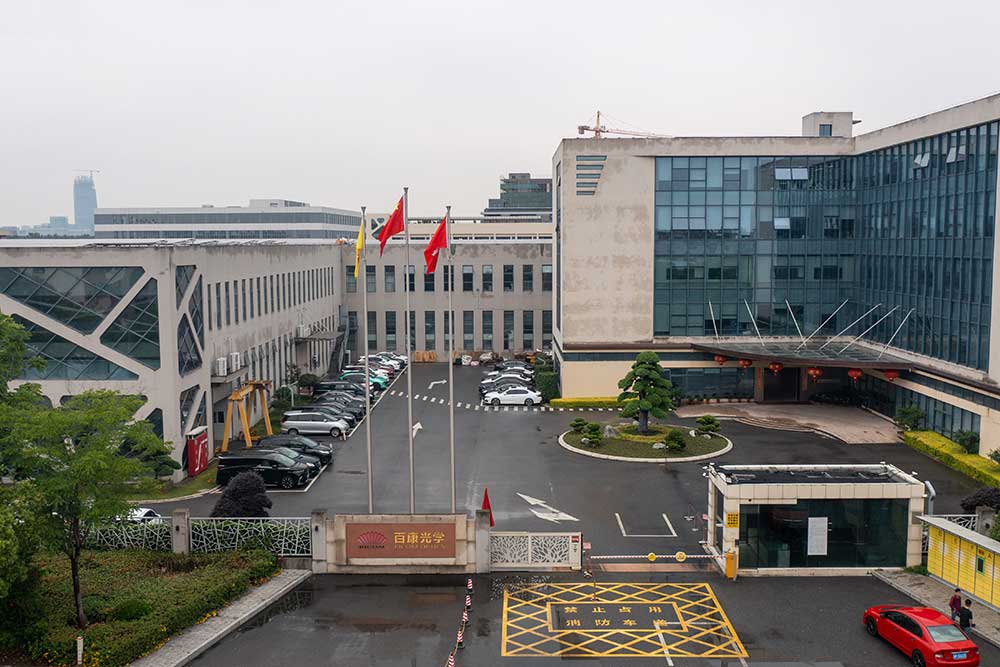
Founded in Shenzhen in 2005, Zhejiang Bicom Optics Co., Ltd. specializes in the precise manufacturing of optical components, focusing on high-quality optical products for the LED lighting, automotive lighting, and security industries. With a robust array of over 130 injection molding machines, BICOM’s annual output value has exceeded 300 million RMB. This success has earned them widespread recognition and cooperation from numerous internationally renowned automotive lighting manufacturers, including Marelli, Hella, and Valeo, continuously showcasing strong growth momentum and market competitiveness.
Recently, we had the privilege to visit BICOM and embark on a journey exploring optics with General Manager Zhou Yun.
1. Optical journey: Customized Solutions Lead Transformation
Since its inception in 2005, BICOM has focused on the design and manufacture of optical components, particularly in the fields of LED and automotive lighting. The manufacturing of optical components demands extremely high precision and stability from the equipment. Facing the market’s stringent requirements for high precision, high transparency, and weather resistance of optical products, BICOM began seeking more specialized solutions.
In 2015, leveraging its extensive technical expertise and profound understanding of optical products, Zhafir custom-designed a series of optical-specific machines for BICOM. These machines not only ensured the optical performance and quality of products like optical lenses but also demonstrated exceptional scalability and stability.
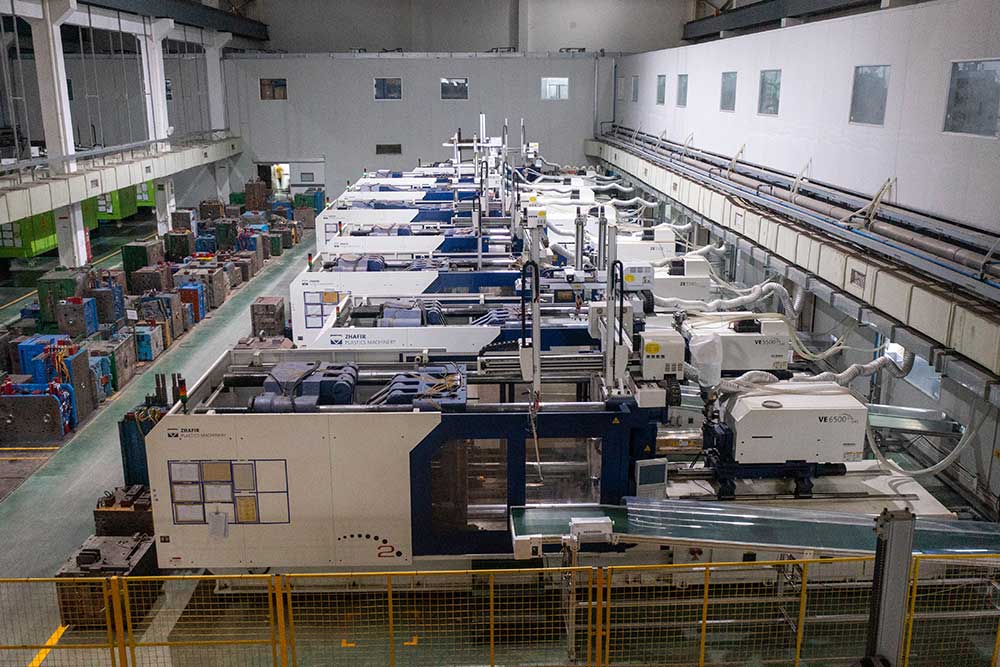

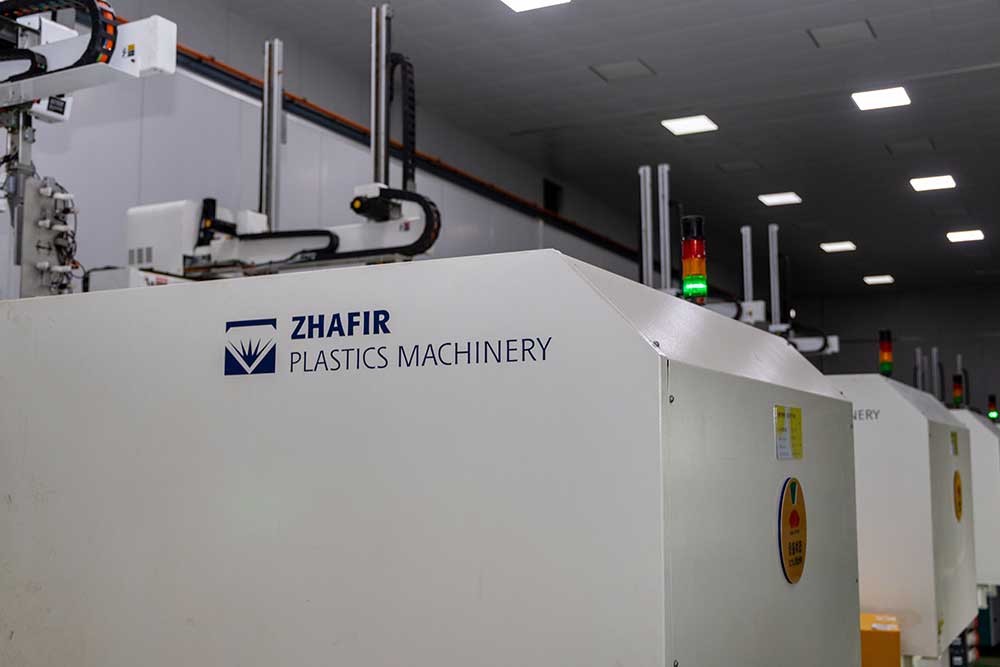
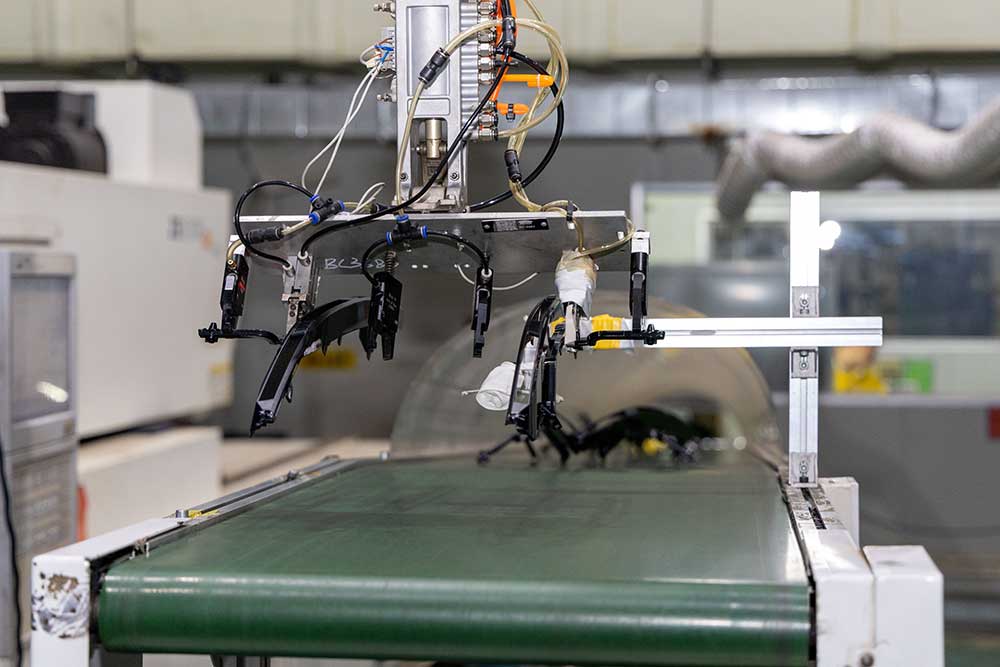
As a result, BICOM began extensively adopting Zhafir’s all-electric optical-specific machines to replace the previous general-purpose injection molding machines. Currently, Zhafir’s all-electric optical-specific machines account for more than half of the factory’s equipment, significantly enhancing production efficiency and product quality, thereby boosting market competitiveness.
2. Specialized Customization: Upgrades in Optical Manufacturing
With the rise of the new energy vehicle industry, the design of automotive light guides has become increasingly complex, demanding higher flexibility and adaptability from injection molding machines. Zhafir’s custom-designed optical-specific machines for BICOM have adeptly met the production needs of irregular molds and transparent optical products. Their specialized design and configuration have brought a qualitative leap to manufacturing.
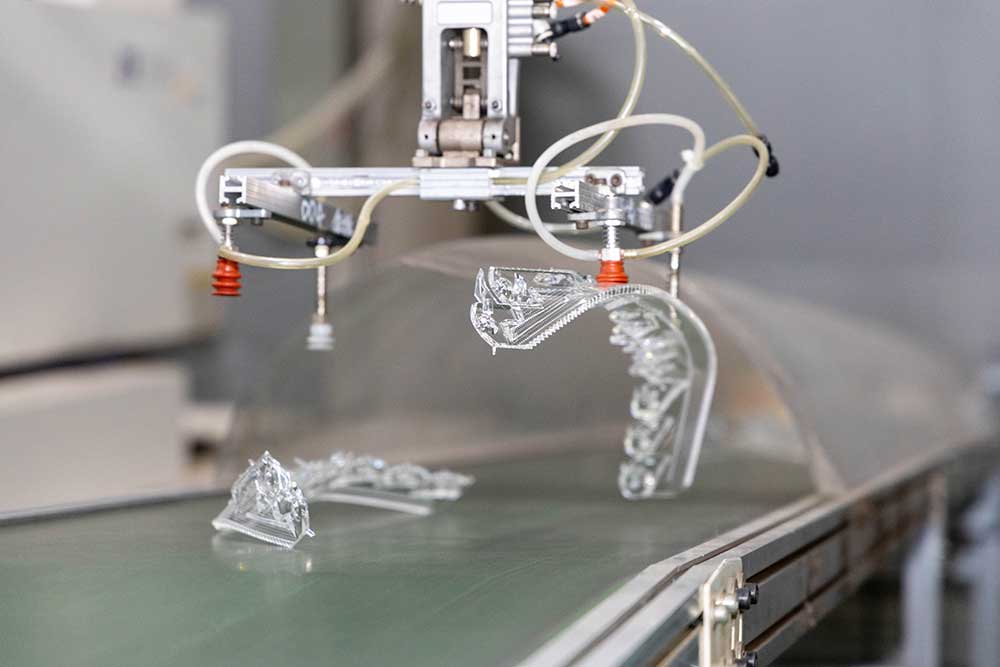
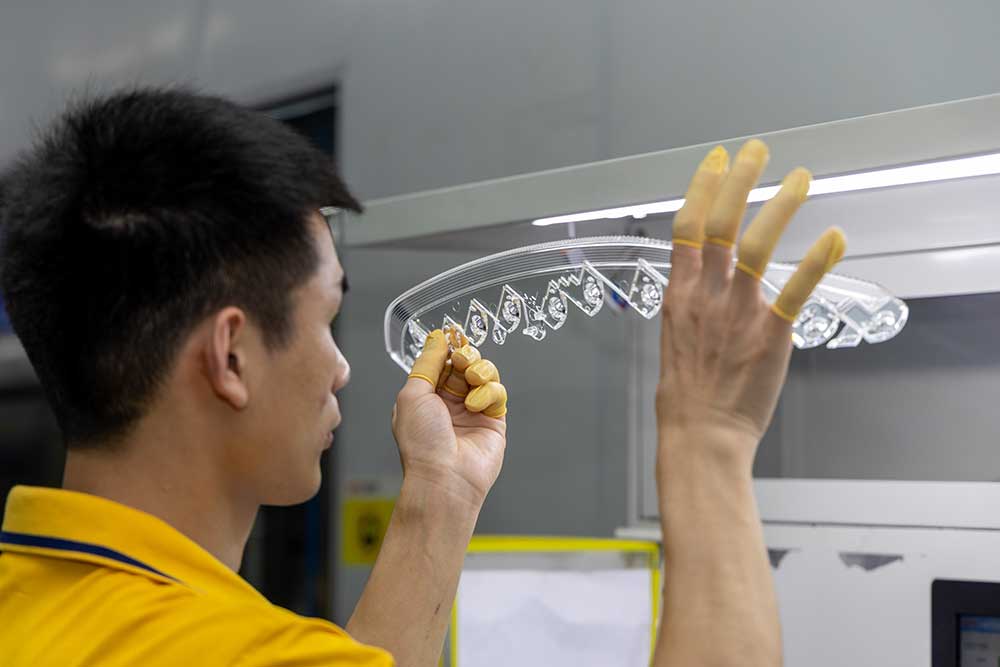
The specialized machines offer not only ultra-large mold capacity but also flexible injection units that can select different screw capacities based on the actual weight of the products, achieving optimal process control. This is particularly important in the light guide industry.
Zhafir’s all-electric optical-specific machines have also undergone customized improvements to core components based on BICOM’s actual usage. For screws, an optical-grade screw was developed to effectively prevent quality issues such as product yellowing and black spots, meeting the high standards of transparency and quality required for optical products. For motors, a high-load design was adopted to address the overheating problem of traditional motors during long-term operation, ensuring the continuity and stability of the injection process. Additionally, this motor design provides strong support for producing thick-walled optical products.
Over the years, Zhafir’s customized services andtechnological innovations have perfectly aligned withBlCOM’s needs. Each upgrade reflects an unwaveringpursuit of optical performance, providing a solidfoundation for BlCOM’s technological leadership andmarket competitiveness in the optical componentmanufacturing field.
At the intersection of light and technology, the storyof Zhafir and BlcOM continues. In the future, we wilcontinue to work hand in hand, tirelessly striving fo)technologicalinnovation,advancing the manufacturing technology of optical components, and continuously exploring newapplications ofinjection moldingtechnology in optics. This collaboration aims to pro.vide new ideas and solutions for the development ofighting systems in new energy vehicles.