Production to the point
2022-10-17
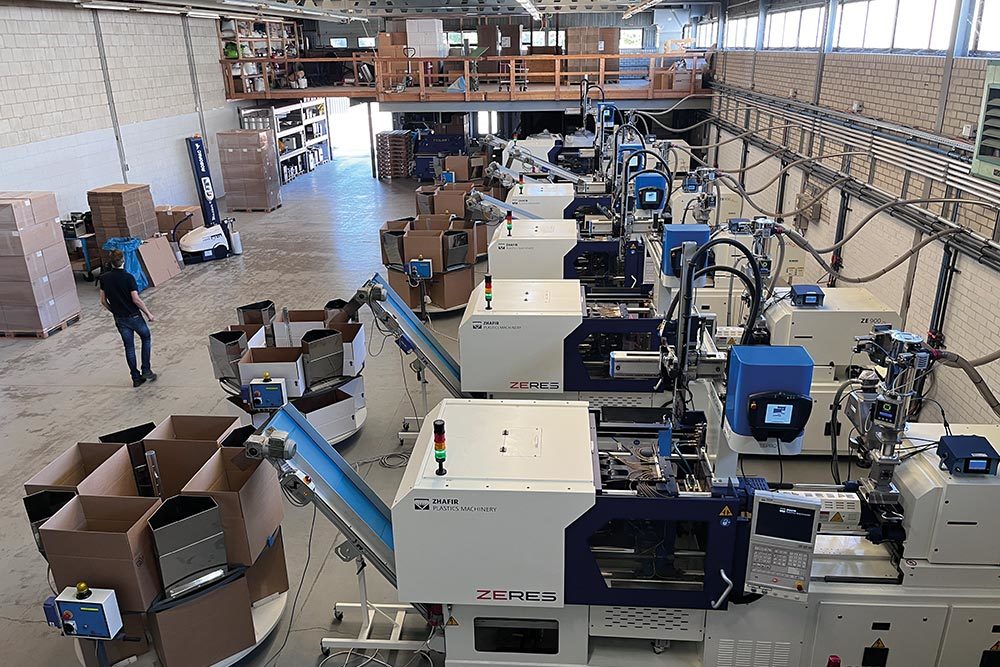
A customer visit to Emperor Mouldings B.V. in Alphen aan den Rijn, the Netherlands.
Brothers Maarten and Peter Keijzer, heads of Emperor Mouldings B.V., embody a new generation of injection molders: focused, efficient and relaxed – with a new understanding of work-life balance. In the Zhafir Zeres Series, they see the best prerequisites for making injection molding processes as efficient as possible and driving production automation forward.
Growing up in his parents’ injection molding business, Maarten Keijzer knew very early on that he wanted to run an injection molding company. The fact that his father then sold the business turned out to be a good decision in retrospect, as Maarten quite inevitably had to found and build up his own company. He took this step in 2019, initially alone, but since 2022 his brother Peter has been completely on board.
Both had precise ideas from the start: “No employees for as long as possible, but to bring production to the maximum, so far that we can still manage everything with just the two of us.” The main products are clips of agricultural use; the end customers are greenhouse operators. In addition to the agricultural industry, they still supply the commodity sector and technical parts. The bottom line is that they focus exclusively on small shot weights in high volumes. This is because highly efficient processes, “production-friendly” products and automation in places where it is worthwhile and serves the work-life balance are important to them. Maarten Keijzer: “I certainly experienced many things in my father’s company that I wanted to do differently. The principle ‘Only those who work hard will make it’ may have had its justification in those days. Today, we have other options. In the age of digitalization and its tools, it’s easier to design efficient and lean processes.” The recently introduced automated foiling of cartons is a good example of this, he said. “This robot saves us a lot of valuable time.” They are currently considering an AGV, which would then take the full cartons out of the magazines at night, increasing piece counts.
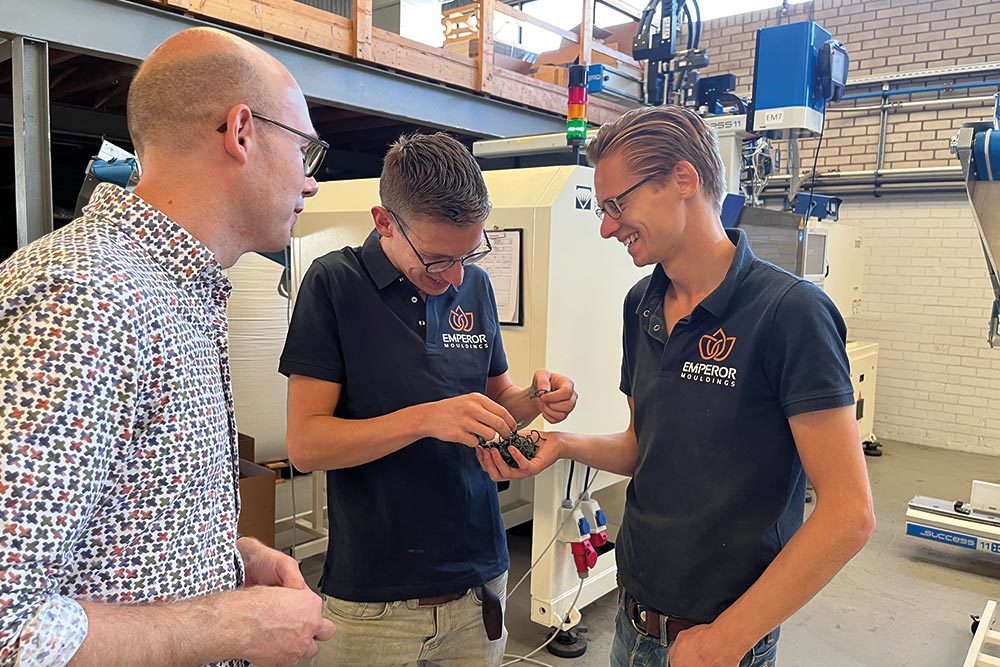
Constantly improving processes: Mark Waterreus (Owner of Robotech, HTIG distributor in NL) talking to the Keijzer brothers.
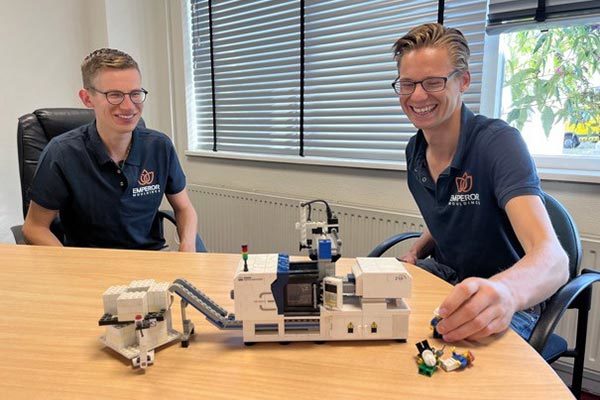
Passion for technology: Maarten (left) and Peter Keijzer with a Venus model made of Lego that they added robotics and peripherals to.
About meaningful growth and scalability
Since its founding in 2019, Emperor Mouldings B.V. has grown steadily, in output, turnover, set-up. “If the demand is there, it would make no sense not to grow,” the Keijzers agree. “But always with moderation and purpose.” Nevertheless, growth is not generally the big goal, they say; rather, they are concerned with the “sporting challenge” of spraying the maximum number of products with the existing machines and their 2-man power. “There is room for eight machines in our production. That’s still a size we can handle with two people. And should the market require more, we’ll see how far we can go with our manpower.”
Growth in this, their sense, presupposes that processes are optimized for maximum efficiency. That cycle times are reduced to the maximum and 24/6 non-stop operation runs smoothly to the maximum, with a clearly focused product group: simple small parts in large quantities.
Accordingly, they have aligned their machinery and supplemented it with pinpoint accuracy. The heart of production is currently formed by five electric Zeres machines with four times 900 and once 1,200 kN clamping force (another is on order). All run with integrated controls (Success Series 7 and 11) from Sepro Robotics. The molds are equipped with external hotrunner systems from PSG, and a specially programmed error-stop function intervenes if the temperature in the metering unit is too high. This also guarantees them near-zero error production at Emperor Mouldings. Original quote Maarten Keijzer: “We’ve had just 1 carton of rejects so far in 2022.”
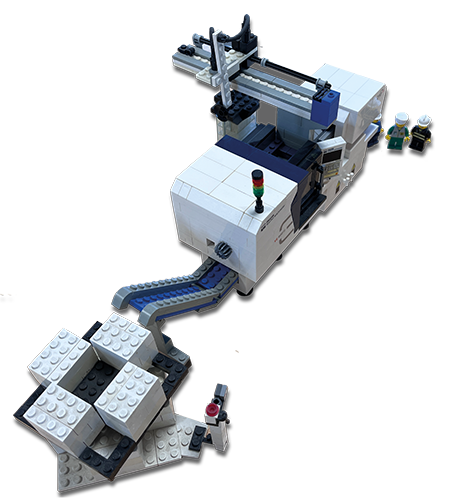
“The electric Zeres fits very well with our philosophy: technology to the point for production to the point. The price-performance ratio is also unbeatable in our eyes. Our first 90-tonne Zeres has already gone through more than 6 million cycles without a significant malfunction.” Maarten Keijzer, Emperor Mouldings B.V.
Performance against rising energy costs
While the young company has come through the pandemic relatively well and relaxed, the energy crisis is having an even more serious impact on its core market, the Dutch agricultural industry. Rising energy prices are likely to bring many greenhouse owners to their knees, by next winter at the latest. “Our warehouse is full and the market is saturated for now. That means that of our machines, only two out of five are currently running. The reason for this is that the agricultural industry is suffering extremely from rising energy prices and many end customers have already announced that they are closing their greenhouses for the winter.” The two brothers nevertheless take the situation calmly: “A crisis is also always an opportunity. Up to now we’ve had full capacity utilization, now we’re using the quiet phase for new customer acquisition, internal projects that have fallen behind, or we’re happy to have more family time.”
Of course, rising energy costs are also making themselves felt in their own injection molding operations, but their stringent decision to use electric machines and the low shot weight of the small parts keep their energy consumption within limits. In any case, they optimize their injection molding processes for maximum energy savings to keep their carbon footprint as small as possible.
First certified industrial compostable clipring made of PLA’
Apart from that, they keep on working on continuous automation of production, keyword: increasing efficiency. “The electric machines are a tremendous help for us to produce in this high efficiency. Our father had hydraulic machines, he still had to ramp them up with some lead time and wait until the oil temperature was right, sort out some cycles of scrap and so on. We turn our Zeres family on Monday morning and don’t turn them off until Saturday night. Machines and the Success line from Sepro are an ideal match. From the first shot, production is error-free,” explains Maarten Keijzer.
In his opinion, another important building block for higher efficiency is material-optimized processes, in which he gained valuable experience in his previous job at a material supplier. “Our injection units are all equipped with a shut-off nozzle, so we can maximize parallel functions during energy-intensive plasticizing. Every second saved has an immediate impact on energy costs.”
In addition to all their commitment to energy savings and efficiency, they are equally consistent in working on their production-side sustainability. From starting with 100% virgin raw material at startup time, they are now at nearly 100% recycled and compostable material.
When asked about concrete visions or dreams for the near future, the answer is rather down-to-earth: “Two days away from the company, but everything continues to run” – that’s a good vision. But of course they are well aware of the challenges ahead and want to face them. And who knows, “maybe we’ll become the smallest smart factory in Europe.”
Info box
Production profile of Emperor Mouldings:
- All Zeres machines run smoothly in 24/6mode;
- All machines are equipped with automation;
- During the day, the machines are serviced and processes optimized if necessary; at night, they produce unmanned;
- Only small parts with a high number of pieces are produced.