Expansiv by conviction
2019-10-31
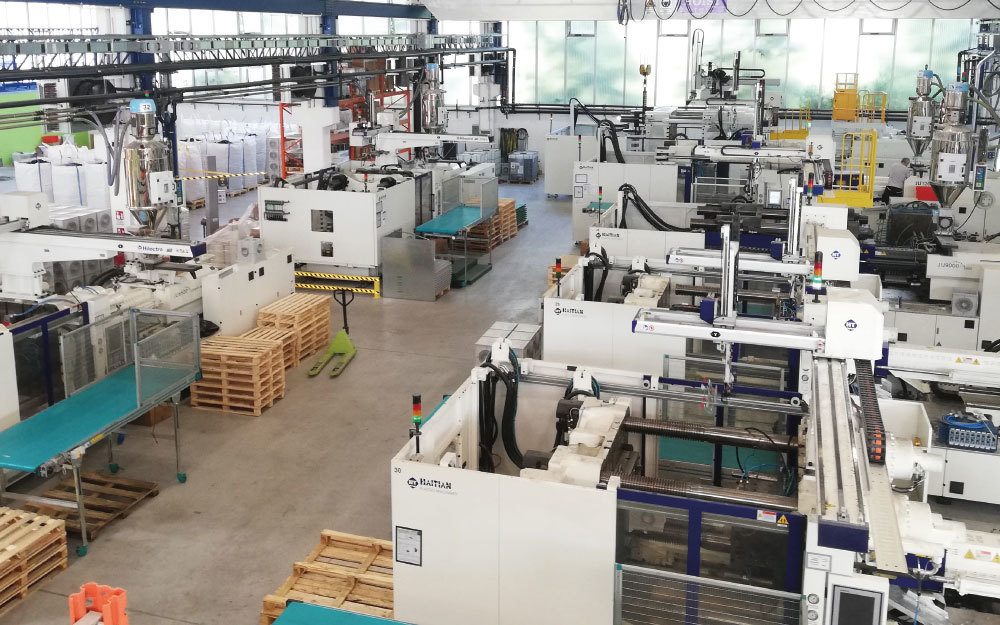
Interview with Zeno Cipriani, Owner of Dakota Group
The Dakota Group is one of the leading companies in the production and sale of construction products. The group has been on an expansion course for about 25 years. Always in focus: progress and innovations for more productivity.
As early as the 1990s, the company was expanding, initially on the domestic market. Subsidiaries in Spain, Portugal and Romania followed. Today, the Dakota Group supplies more than 4,000 customers worldwide. The product portfolio includes drainage and grating systems, drainage systems, dock levellers and much more. Products for the automotive, packaging and the pharmaceutical industry complement the portfolio.
Dakota’s management believes that they have been created for major tasks. By continuously investing in both new technologies and qualified employees, Dakota aims to provide a powerful infrastructure for the challenges of the future. The owner sees energy-efficient, automated and highly productive manufacturing systems as the key to success.
Mr. Cipriani, you have been a Haitian customer since 1998. Which criteria were decisive for you at that time?
“The overall concept convinced us, and it still convinces us today. All Dakota products are made with Haitian and Zhafir machines.”
Which series do you own?
“The Zeres, Venus and Jupiter. Most of them are from the Zeres Series.”
What products does Jupiter manufacture?
“We are currently producing a Smart Catch-Pit, a robust hollow body made of PP. We produce it on a Jupiter with 650 tons. The product varies in sizes from 200 x 200 mm to 550 x 550 mm.”
To what extent do you use automation in your production?
We use central systems for material feeding and drying, as well as internal and external centralized containers for the warehouse. In total, we have about 40 Hilectro robots, six-axis robots, assembly machines, automatic packaging and storage machines”.
Do you also use recycled material?
“We have been focusing on the recovery and reuse of plastic waste generated during production for a very long time. At the same time, we are systematically working on reducing microplastics.”
What do you think which drive will shape the future?
“Certainly the electric one, especially since the electric machine reduces energy consumption and guarantees higher energy efficiency. Apart from that, we have been using self-produced energy for some time, through our photovoltaic systems in production and logistics. Solar energy can also reduce energy costs”.
Do you already integrate digital concepts into production?
“In fact, we can say that Dakota has been a smart factory for 15 years. We have been using the 4.0 concept since 2005. Each injection machine is connected to the central server. All data and processes are registered by the main computer and all information is exchanged between the branch, office and production. These activities are a must for 24/7 operation and a modern factory.”
DAKOTA GROUP – Facts & Figures
Location: Headquarter in Italy
Subsidiaries in Spain, Portugal and Romania
Revenues: EUR 50 million turnover p.a.
More than 100 employees
24/7 Production
approx. 120 machines from 60 to 2000 t
Raw materials: PP,PA,PE,POM,ABS,PS,
PLA, ASA,TPE 30,000 t Raw material
consumption p.a.
The Dakota Group has been a member
of the Green Building Council Italia since
January 2019. The GBC network
promotes the culture and practice of
sustainable building.
www.dakota.eu