Machine Core Functions
Injection Speed
low and high injection speed as general basis for good filling criteria of the molding parts
A high injection speed combined with strong dynamics is important for an adequate filling capacity for thinwalled moldings. The switchover to holding pressure must also be repeatable and bring a rapid decrease in pressure, so that the injection process can be sustained at high injection pressure to extend as great as possible, until filling is complete.
With particularly thick-walled moldings (starting from approx. 4-5 mm wall thickness), very slow speeds are required, that are lowered reproducibly. The diagram to the right shows the injection speed over time for two machines at a maximum injection speed of 120 mm/s.
SPEED / PARALLEL MOVEMENTS
as general basis for short cycle times
In principle, the attainable cycle time with all moldings is a relevant measurement for assessing the machine functions.
Nevertheless, with short cycle times (< 10 s) the achievable savings in cycle time carry proportionately more weight.
EXAMPLE: SIMPLE PARTS
The diagram shows a cycle time comparison between Mars II and Venus II producing ski bindings made of PA6-GF30 in a cycle time of 45 s.

ENERGY CONSUMPTION
as general basis of a good filling criteria of the mold parts
Rising energy costs make it increasingly necessary to take the expected energy consumption into account, when making a purchasing decision. It is not possible in this case to assign clearly into part groups.
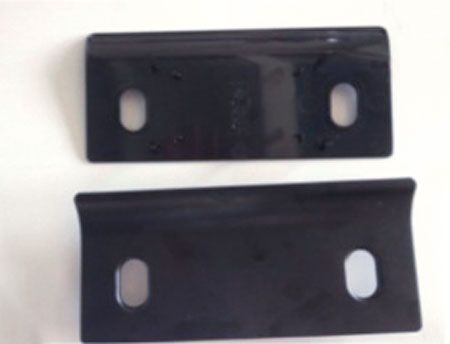
EXAMPLE: SIMPLE FUNCTIONAL PARTS
The diagram shows an energy comparison between Mars II and Venus II producing simple functional part (automotive cover) for Audi made of PC/ABS in a cycle time of 23 s.


PRECISION
as general basis for reproducible weights, size accuracy and warpage
For moldings requiring high precision, a priority is placed on the reproducibility of the machine functions, especially for those moldings assembled later or automatically processed afterwards. The closing performance of the backflow shut-off valve, the repeatability of the injection movement at the start of injection, the injection stages, and the switch-over to holding pressure have significant influence.
The weight of the finished molding indicates very well the degree of precision of the machine functions interacting together. Small variations in weight indicate, that the machine functions are performing well and reproducibly. The graph above compares the weight spread obtainable from the Mercury and the Venus machines.
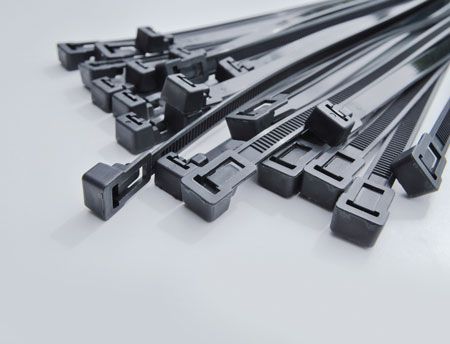
EXAMPLE: PRECISION PART (THINWALLED)
The diagram shows precision comparison between Mercury and Venus II producing a thinwalled precision part (cable tie) made of PA12 in a cycle time of 12 s.

ME 550
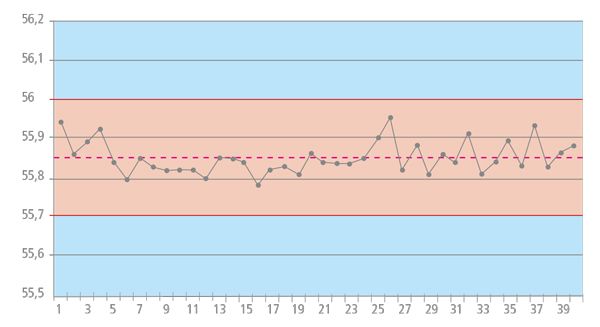
VE 900 II