Haitian Plastics Machinery and Leapmotor Celebrate First Successful Production of Resin Line Bumper Project
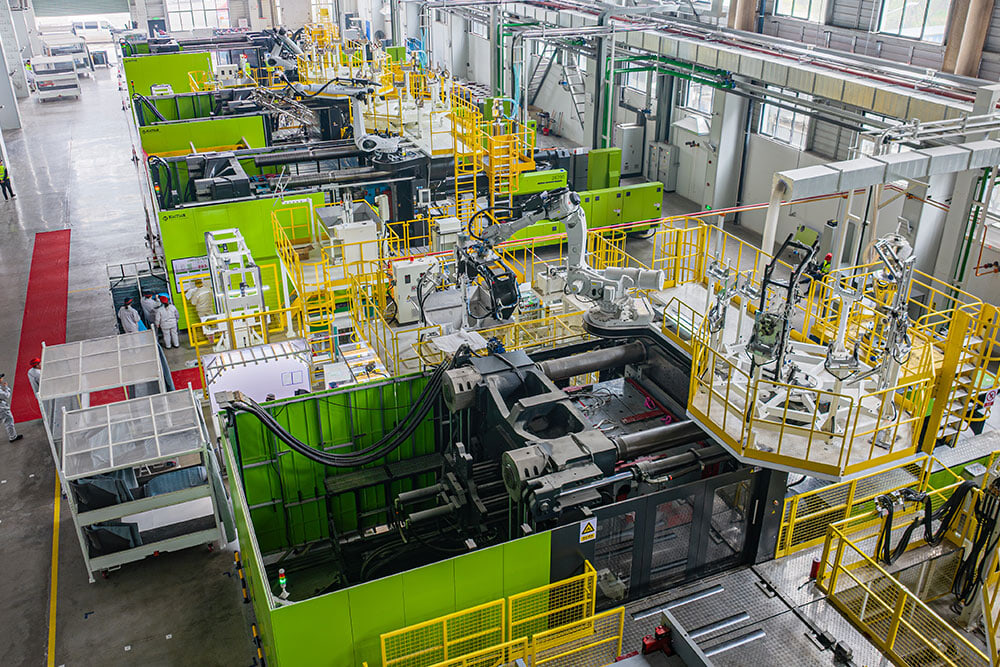
On March 10, the first product of the resin production line bumper project, a collaboration between Haitian Plastics Machinery and Leapmotor, successfully rolled off the production line at Leapmotor’s Jinhua production base in Zhejiang. This milestone marks a solid step forward in the deepening cooperation between the two companies in the automotive parts sector. It also resonates with Leapmotor’s same-day announcement of its LEAP 3.5 technology architecture and the B10 model pre-sale launch, jointly reinforcing the brand promise of delivering „high quality, high configuration, and smart electric vehicles for everyone.“
At the roll-off ceremony, key representatives from both sides attended to witness this important moment, including Dai Bin, Deputy Director of Technology and Quality for Leapmotor’s Resin Production Line, Xiao Dasheng, Senior Manager of Production, Xu Bin, Vice General Manager of Haitian Plastics Machinery’s Global Industry Line, Liu Lizhu, Sales Manager of Northern Zhejiang Region, and Hu Haibo, Key Account Customer Service Manager.
The bumper produced during this milestone event was manufactured using Haitian’s HA33000-20200 ultra-large injection molding machine. With an injection equivalent of 20,200 and equipped with a high-efficiency, high-wear-resistant B-150mm screw, the machine is specially designed to handle the complex structures of new energy vehicle (NEV) bumpers. The bumper weighs 3,470 grams and is molded efficiently using a single-cavity PP molding process. Integrated with advanced automation technologies—including mold transfer carts, magnetic platens, six-axis robots, gate cutting systems, automated weighing, jig exchange platforms, laser marking, AGV transportation, and vertical storage systems—the production line achieves fully intelligent operation from raw material delivery to precision molding and post-processing.
Moreover, the equipment’s high-rigidity clamping system, intelligent mold opening and closing function 2.0, and IPO injection algorithms ensure the precision molding of Leapmotor’s rear bumpers. This injection molding solution not only offers high precision and efficiency but also excels in energy savings and space optimization, enabling Leapmotor to produce high-quality bumpers more efficiently and economically, further reducing the overall vehicle cost and making smart electric vehicles more accessible to a broader consumer base.
It is worth noting that this first production coincided with the global pre-sale launch of Leapmotor’s B10 model. As a pioneer committed to making smart electric vehicles accessible to all, Leapmotor continues to adhere to the vision of „bringing intelligent technologies from luxury exclusivity to everyday necessity, making advanced smart driving within reach for everyone.“
As a leader in the injection molding equipment industry, Haitian Plastics Machinery is dedicated to providing customers with highly efficient, energy-saving, precise, and cost-effective injection molding solutions. This cooperation represents the perfect synergy of both companies’ pursuit of high-quality manufacturing and technological democratization. Moving forward, Haitian and Leapmotor will continue to resonate on the same frequency, working hand in hand to drive the sustainable development of the smart electric vehicle industry, delivering more high-quality and affordable products and services to end consumers.