Reydel Automotive Slovakia s.r.o.
2016-10-05
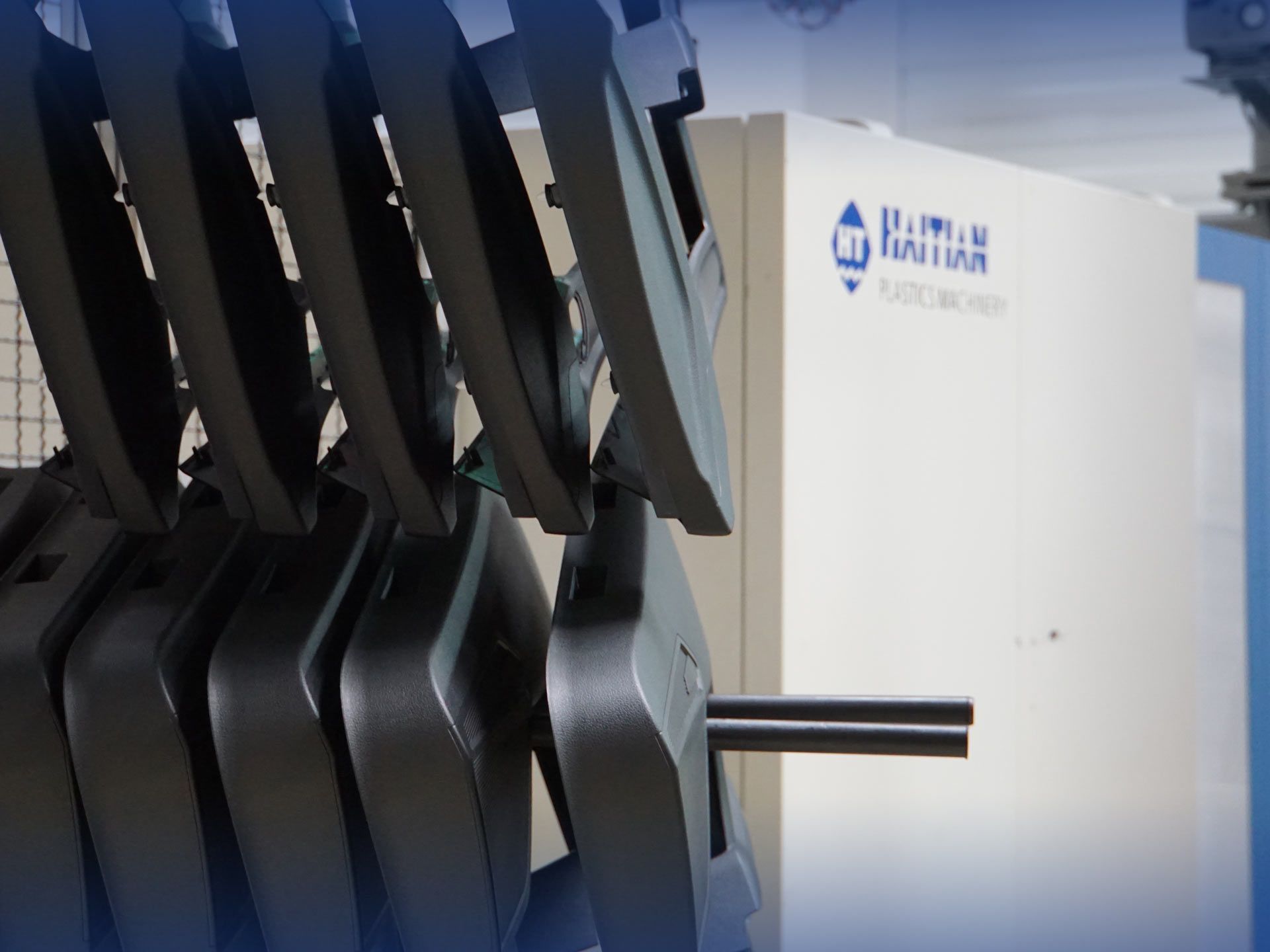
Haitian Jupiter II Serie: “DIE JUPITER II HAT SICH BEWÄHRT”
Als T1-Supplier ist die Reydel Automotive Slovakia s.r.o. spezialisiert auf hochwertige Innenraumteile, hauptsächlich für Cockpits. Das Produktionsspektrum reicht von Armaturenbrettern über Be- und Entlüftungen bis hin zu Türleisten. Wir unterhielten uns mit Milan Vecera, Manufacturing Manager bei Reydel in Nitra, über den Stellenwert der Flexibilität für die Fertigung just-in-time.
Der Standort Nitra beschäftigt 380 Mitarbeiter und produziert in 4 Schichten 7/24. Das Produktionswerk umfasst aktuell 21 Spritzgießmaschinen von 320 bis 2800 t, darunter 5 Haitian Jupiter II Serien (von 4.500 bis 28.000 kN). Verarbeitet werden meist Standard-Materialien wie PP, HCPP, PAGF, ABS und PC/ABS, mit einem Gesamtvolumen von ca. 4.000 – 4.500 t im Jahr. In der Automatisierung setzt Reydel auf Lösungen von SEPRO.
Reydel Automotive Slovakia ist Haitian-Kunde seit April 2014. Das Headquarter der Reydel Gruppe befindet sich in Frankreich und unterhält regionale Engineering Centers in Europa, Asien und Südamerika sowie “JIT” (just in time) Fertigungsstätten nahe der OEMs in West- und Osteuropa, Asien, Südamerika sowie Marokko.
Herr Veĉera, wir beobachten bei unseren globalen Kunden aus der Automobilindustrie, dass der Trend weg geht von hochkomplexen Fertigungszellen – sehr produktiv, jedoch speziell für das eine Kunststoffteil ausgelegt. Mittlerweile muss der Zulieferer sehr flexibel in seiner Produktion sein, um auf Facelifts und daher auf schnelle Werkzeugwechsel, immer kürzere Produktlebenszyklen oder Kurzfristige Sonderprojekte der OEMs reagieren zu können. Was ist Ihre Meinung dazu, und was erwarten Sie von Ihrem Maschinenlieferanten?
„Ja, der Druck von den OEMs an T1-Suppliers ist enorm. Die Produkte werden von Tag zu Tag immer variantenreicher und haben sich bei manchen OEMs sogar verdoppelt. Das hat Einfluss auf Manpower und Maschinenverfügbarkeit, beide Faktoren brauchen z.B. Lösungen für schnelle Werkzeugwechsel.“
Wie komplex sind Ihre Fertigungszellen aufgebaut?
„Unsere Fertigungszellen enthalten den Spritzgussprozess, Work in Progress, ASSY, also Baugruppenmontage mit finaler Kontrolle und den Versand. Einige Teile werden mit “Soft Touch”, andere mit schwarzem Hochglanz-Klavierlack versehen. Die ASSY ist dabei der komplexeste Teil der Fertigungsstraße. Üblicherweise beinhaltet sie die Vormontage wie Ultraschall-Schweißgeräte, Vibrations-Schweißen, Infrarot-Schweißen, die Laser-Perforation fürs Armaturenbrett mit Airbag sowie Press-, Schneid- und Klebemaschinen, um mit Textilien oder Leder zu dekorieren.“
Ihre Direktorin Ing. Jana Bogyóová sagte in einem Interview, dass die Produktion für Trnava “just in sequence” erfolgt. Was bedeutet das für Sie als Manufacturing Manager?
“Just in sequence bedeutet in Wirklichkeit ein einfaches Leben für unsere Kunden, ist jedoch ein harter Job für uns. Eine Produktion für den Peugeot 207 erklärt das ganz gut: Am Band bei PSA in Trnava passiert das Auto eine Station, welche mit uns in Verbindung steht. Wir erhalten also eine Beschreibung der erwarteten Türpanelen in diesem Fall schwarze Türen mit rotem Textil und so weiter, unsere Kommissionierung erfasst die Anfrage, holt aus dem Lager die fertigen Spritzgussteile, gibt sie in den ASSY-Fertigungsprozess, etikettiert sie und legt sie an die korrekte Stelle im Rack ab. Vom Zeitpunkt der Bestellung bis zur Lieferung an das Band bei PSA haben Sie 183 Minuten. Egal ob es schneit, Ihr LKW einen Unfall hat oder sonst etwas passiert: Wenn Sie nicht pünktlich liefern, wenn die Teile sich in einer falschen Position auf dem Rack befinden oder das falsche Etikett tragen, verlässt das Auto das Band und Sie zahlen. Rund 500 Euro pro Minute. Das ist unser Geschäft und unser Risiko.“
Haitian International fokussiert mit “Technologie auf den Punkt” genau auf diese Balance zwischen Flexibilität und Produktivität, bietet Spritzgießmaschinen mit einem hohen Standard, ausgestattet mit umfangreicher Software, allen gängigen Schnittstellen und der Möglichkeit, jede Menge Optionen als Hardware hinzuzufügen. Um maximale Flexibilität und eine weite Fertigungsbreite an Teilen zu ermöglichen. Welche Erfahrungen haben Sie bei Reydel mit dieser Technologie auf den Punkt gemacht?
„Wir arbeiten nun seit 1,5 Jahren mit den Jupiter II Maschinen ohne nennenswerte Zwischenfälle. Es gab Kleinigkeiten, aber die haben wir gelöst. Technisch gesehen ist die Jupiter II auf dem exakt gleichen Niveau wie entsprechende Wettbewerbsmaschinen. Sie haben sich seither bewährt und werden bei uns daher in ihrer Funktionalität in keinster Weise in Frage gestellt. Im Gegenteil. Alle Komponenten der Jupiter sind international bekannt. Rexroth, Mitutoyo, ABB, usw. Viele der Ersatzteile sind sogar frei am Markt erhältlich. Die transparente und offene Strategie von Haitian begrüßen wir sehr. Und die Steuerung von KEBA Österreich ist uns sehr gut bekannt. Alles in allem kann ich sagen, dass die Maschinen das liefern was wir erwarten. Brauchen wir mehr, fragen wir.“
Welche Anwendungen laufen hauptsächlich auf den Jupiter Maschinen?
„Türleisten auf Tandem-Werkzeugen, Armaturenbretter, Airbags und andere kleine Komponenten.“
Wie bewerten Sie die Zusammenarbeit mit Haitian International, und was war ausschlaggebend für die Kooperation?
„Es hat damit angefangen, dass wir einen Transport alter Maschinen vermeiden wollten. Die Kosten für Reparatur und Transport waren genauso hoch wie der Neupreis der Jupiter mit etwas weniger Schließkraft. Ich hatte keinerlei Erfahrung mit Haitian, aber alles mit 2 Jahren Garantie ist besser als alte Maschinen mit Öl-Leckagen. Also entschied ich mich für die Jupiter, und das bereue ich bis heute nicht. Nach der ersten Maschine begann dann eine gute Partnerschaft. Das Team von Haitian reagiert sofort, z.B. bei Systemänderungen, Maschinenadaptionen, etc. Das ist nicht üblich in Europa. Das Bediensystem ist offen in allen Ebenen, wir sind also die absoluten Besitzer und können alles programmieren was wir wollen. Natürlich birgt diese Art von Freiheit eine gewisse Gefahr. Man hat umfassenden Zugriff, ist aber auch für das Ergebnis verantwortlich. Meiner Meinung nach ist es eine gute Strategie, insofern man weiß, was man tut.“
Welche Antriebskonzepte präferieren Sie?
„Wir haben uns auf Servo-Antriebe eingeschossen. Die ermöglichen ca. 60 % Kostenersparnis an Elektrizität im Vergleich zu den klassischen Antrieben. Und das Zwei-Platten-Design spart uns Platz in der Produktion. Das nennen wir Technologie auf den Punkt.“